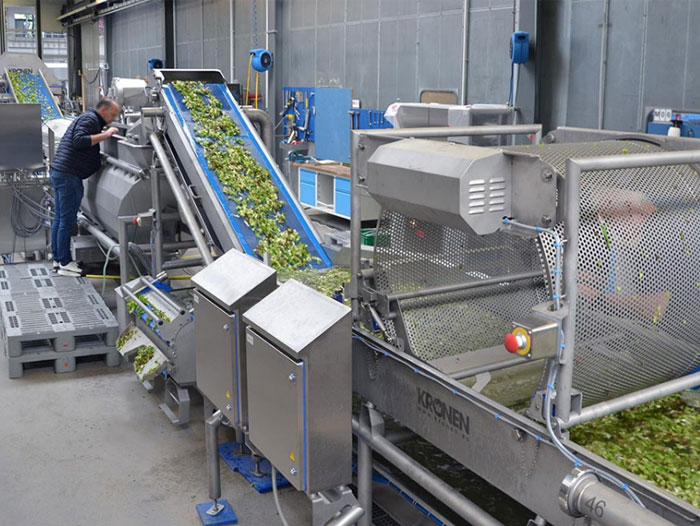
A rare special occasion: within the scope of a major order, the company KRONEN in the German town of Kehl am Rhein is manufacturing four processing lines, one of which was recently demonstrated live to an audience of interested guests invited by KRONEN. The automated, networked line is the third of the four lines that make up the order. Two of the lines are already operating in the facilities of the fresh produce manufacturer, and the other two will be installed by the end of the year. The processing lines boast state-of-the-art technology and set new standards, above all with regard to hygiene. The demonstration offered the visitors from throughout Europe, Latin America and the US the opportunity to experience the innovative system close up and in action while it processed a product.
The processing line, which forms part of a large-scale order, is currently located in KRONEN’s production hall in the town of Kehl by the river Rhine. Just like the fourth and final line of the order, it will be installed at the facility of its new owner, a manufacturer of fresh produce, by the end of the year. Two of the lines have already been in operation at the company since the start of the year. “We were determined to offer our customers and interested visitors the opportunity to experience this new processing line live and fully functioning, namely with an actual product, before it enters into operation,” explains Stephan Zillgith, spokesman of the KRONEN Board of Management. “We therefore invited companies from the fresh-cut industry to the demonstration and were delighted about the abundance of interest shown by the participants from Germany, Switzerland, Norway, the Netherlands, Mexico, Belgium, and Poland.”
A variety of live demonstrations were held on site at the KRONEN facility in Kehl throughout September. What’s more, an online demonstration via a live broadcast was provided for representatives of around 50 companies from Latin America and the USA, who were unable to attend in person. The KRONEN project team presented the innovative processing line to customers and interested companies from the fresh-cut industry in a number of individual guided tours and discussions. “From our perspective, the demonstration of the new, networked processing line was highly worthwhile: it was an excellent opportunity to experience such a line actually processing a product. It enabled us to discover KRONEN’s expertise in creating automated systems live and in person. We were particularly impressed by the integrated GEWA XL washing machine,” stated one of the participants.
Intelligent and efficient weighing, washing, drying, and sorting
The customer plans to use the processing line for salad leaves, salad mixes, and leafy vegetables to process up to 1,000 kg of baby leaf lettuce or the equivalent amount of mixed lettuce per hour. The line combines innovative washing and drying technology from KRONEN with dynamic weighing systems and mechanical and optical sorting solutions from KRONEN partners. It contains a variety of new and further developed machines, including the K850 drying system, the GEWA AF pre-washing machine, and the GEWA XL HELICAL washing machine. What’s more, recipe weighing belts from Synergy Systems and a mechanical sorting system and UVC treatment system from HiTec Food Systems are also integrated into the line.
All of the components in the processing line are networked. The communication between the machines and the visual displays for the machine operators help to facilitate a reliable, constant, and uninterrupted production flow. In turn, this fully automated, continuous processing enables the line to only require a small number of staff and to achieve a cost-efficient processing procedure. Last but not least, it guarantees high processing capacities and maximum hygiene and quality in production.
GEWA AF, GEWA XL, and K850: gently processing large capacities
The GEWA AF is a pre-washing machine that uses a washing system newly developed by KRONEN. It was specially developed to wash floating, leafy products, to submerge light, delicate products without mechanical stress, and to handle production peaks. The GEWA AF uses a completely new and unique principle: the “Active Flume” (AF) washing system. Compared to HELICAL washing machines, the water-to-product ratio of the GEWA AF is only four liters of water for one liter of product, and this 4-to-1 ratio is perfect for pre-washing. The machine is able to remove cell sap, sand, and soil. The standard version of the GEWA AF requires a total of 1,400 liters of water. It washes baby leaf lettuce at a capacity of 400 to 1,500 kg per hour. The GEWA AF can process iceberg lettuce at a rate of up to 3,000 kg per hour and baby spinach at up to 1,000 kg per hour.
The GEWA XL is equipped with a HELICAL washing system especially for large processing capacities. After pre-washing, a HELICAL washing machine like the GEWA XL, which uses a spiral-shaped rotation process and 2,600 liters of water, produces optimum washing results in a second stage. With the GEWA XL, baby leaf lettuce, for example, can be washed at a rate of up to 1,500 kg per hour. Iceberg lettuce, on the other hand, is gently processed at a rate of up to 5,000 kg per hour.
With its GEWA AF and GEWA XL washing machines, KRONEN is bringing new standards of hygiene to the market. To allow users to clean the pipe system without dismantling it, a “Clean in Place” system can be optionally integrated. This intelligent solution feeds the chemicals through the pumps and pipes, thus further reducing the volume of water required for the cleaning process. What’s more, the GEWA XL can be completely disassembled to gain access to the entire machine.
The K850 drying system for dewatering cut vegetables, fruit, and lettuce, as well as whole leaves, is a further development of KRONEN’s K650 drying system. When upgrading the system, KRONEN focused on aspects such as the drive system, increased capacity, and optimized hygienic design. It deliberately gave the K850 a low infeed height compared to the size of the machine. As a result, the length of the infeed belt is shorter and therefore saves a considerable amount of space with regard to the set-up area of the large-scale system. The system is comprised of an infeed buffer belt, a centrifuge, an outfeed belt, and an external control cabinet. The parameters in the programs were extensively automated so that the settings are clear and the system is easy to operate. The fully automated system processes up to 5,000 kg per hour in a continuous processing procedure.
Video of the processing line: www.kronen.eu/line-preview-video
About KRONEN GmbH
KRONEN is a family-managed globally operating producer and supplier of stand-alone machines, special-purpose machines, and high-tech processing facilities for the fresh-cut industry. The product program of KRONEN and its partners covers fruit, vegetable, and salad processing: from preparing, cutting, washing, drying, dewatering, peeling, and sterilizing right through to packaging. KRONEN additionally offers technical solutions for meat and fish, baked goods, ready meals, dried and frozen products, and pet food.
The company, which is based in the German town of Kehl am Rhein and has a second production site in the nearby town of Achern, currently employs more than 120 members of staff, has representations in more than 80 countries worldwide, and supplies its products to over 120 nations all over the globe.
With more than 40 years of experience in food technology, KRONEN preserves traditional values such as quality awareness and relies on a sustainable, holistic approach for the hygienic, reliable production of healthy food. KRONEN considers itself to be a think tank that provides innovative solutions to benefit its customers and meet all their needs. It guarantees top-quality advice and planning expertise in close cooperation with the industry and research establishments.